工业控制软件:效率与灵活性的矛盾何解?
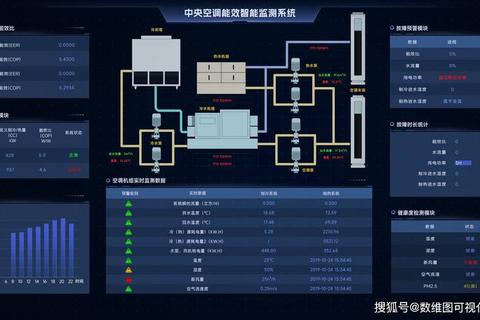
在工业4.0浪潮下,某食品加工厂曾因传统PLC编程耗时6个月无法完成产线改造,导致错过旺季订单;另一家汽车零部件企业则因设备品牌混杂,系统集成费用超预算200%。这些真实困境折射出工业控制领域的两大痛点:开发效率低下与跨品牌设备协同困难。当"灵动高效新标杆:昆仑通态组态软件智启工业控制新时代"打破传统模式,用可视化组态技术将产线改造周期缩短至3周,这场工业控制领域的效率革命正引发行业深度思考。
1. 如何让工业控制开发效率提升50%?
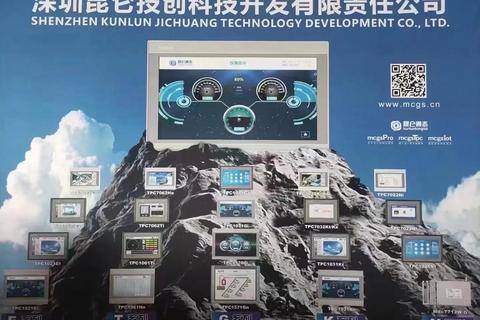
某搅拌设备制造商的应用案例极具代表性。传统开发模式下,工程师需要编写2000行PLC代码实现物料罐液位控制、阀门联动等基础功能,耗时超过45天。而采用昆仑通态组态软件后,通过可视化拖拽元件库中的传感器、电磁阀图形,配合实时数据库配置,仅用21天就完成了包含3D动画监控、异常报警策略的完整系统开发。
这种效率跃升源于三大技术创新:首先是模块化元件库,软件内置2000+工业设备图元,涵盖从称重传感器到机械臂的完整产线要素;其次是实时数据库技术,数据处理效率达每秒400万条读写,确保设备状态同步延迟低于50ms;更关键的是"所见即所得"的动画组态功能,工程师可通过液位升降效果预览直接关联设备变量,避免传统反复烧录调试的耗时环节。
2. 如何实现跨品牌设备无缝对接?
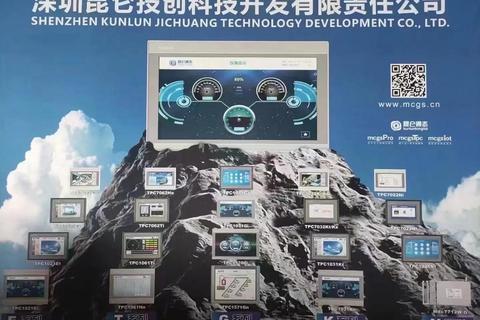
在浙江某光伏组件工厂,7种不同品牌的PLC、5类进口仪表和3套国产DCS系统的整合曾让工程师束手无策。昆仑通态组态软件通过三层架构破解了这个行业难题:底层设备层兼容Modbus、OPC UA等23种通讯协议,中层数据处理层实现毫秒级数据归一化,上层应用层提供统一可视化界面。最终该厂设备互联成本降低60%,异常响应时间从30分钟缩短至90秒。
软件支持的设备名录印证着其开放性:从西门子S7-1200到三菱FX系列PLC,从霍尼韦尔传感器到台达变频器,覆盖全球95%主流工业设备。更值得关注的是其"设备无关"设计理念,当某纺织企业需要新增欧姆龙视觉检测系统时,仅需在设备工具箱拖拽对应驱动构件,无需重写核心逻辑。
3. 智能化升级能否让传统产线焕发新生?
山东某水泥厂的转型最具说服力。该厂在保留90年代核心设备基础上,通过昆仑通态组态软件构建的智能监控系统,使吨能耗降低12.7%,设备故障预测准确率达89%。系统集成的工艺顺控器模块,将生料配比精度从±5%提升至±0.8%,每年节省原料成本超300万元。
这背后是软件深度嵌入的智能算法:模糊PID控制模块使温度波动控制在±0.5℃,多变量预测模型实现72小时故障预警,而基于SQL Server的历史数据分析,可自动优化生产节拍。在广东某PCB板厂,软件集成的视觉检测模块使产品缺陷漏检率从1.2%降至0.03%,每年减少质量损失800万元。
工业智能化的实践路径
灵动高效新标杆:昆仑通态组态软件智启工业控制新时代"的实践表明,企业智能化转型需把握三个关键:首先建立设备数字画像,通过软件的数据采集功能完成产线"体检";其次采用渐进式改造策略,优先实施能耗监测、预测性维护等见效快的模块;最重要的是培养"软件定义设备"思维,将组态平台作为生产系统的数字底座。
建议制造企业分三步走:初期选择搅拌机、包装线等标准化单元进行试点,中期构建跨车间数据中台,最终实现全厂数字孪生。某乳制品企业正是沿此路径,用18个月完成从单机数字化到智能工厂的跨越,验证了组态软件作为工业数字化转型核心工具的价值。在智能制造的新赛道上,选择适配的软件平台,就是选择未来十年的竞争力。