当传统工厂还在“人海战术”,智能化管理是解药还是?
制造业的老板们常陷入两难:一边是逐年攀升的人工成本、原材料浪费和设备维护费用,另一边是客户对交货周期和产品质量的苛刻要求。有人质疑:“花大价钱上管理系统,万一效果不达预期,岂不是雪上加霜?”这种担忧不无道理——据某行业协会统计,约40%的中小企业在数字化转型中因选型失误或实施不当而陷入停滞。但另一组数据却显示,成功应用智能工厂管理系统的企业平均生产效率提升35%,成本下降20%以上。矛盾背后,真正的症结在于:如何让管理软件真正“懂”工厂?
一、数据孤岛如何打破?
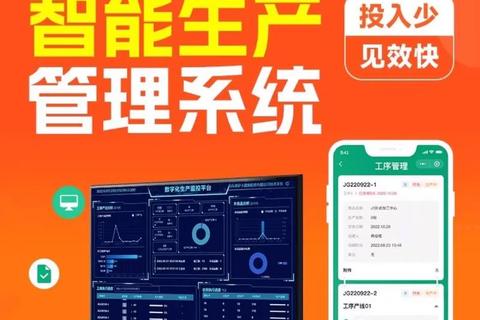
传统工厂的痛点往往始于数据割裂:生产进度靠口头汇报、库存数据依赖手工盘点、设备状态凭经验判断。这种“盲人摸象”式管理导致决策滞后和资源浪费。
以三一重工18号灯塔工厂为例,其通过MES与ERP系统无缝集成,实现从订单到交付的全流程数据互通。客户下单后,系统自动分解生产任务,实时追踪物料库存和设备状态。例如,当某台机床的传感器检测到刀具磨损超标,系统会立即触发预警并调度备用设备,避免产线停滞。这一改造使该工厂产能提升123%,单位成本降低29%。
另一典型案例是烘焙品牌法派1855。过去其门店浪费率高达15%,因过期商品无法及时预警。引入海致BDP系统后,通过实时分析销售与库存数据,系统自动生成动态补货建议,并将浪费率关键指标推送至店长手机。仅半年时间,浪费率下降10%,毛利率增长7%。
二、流程黑洞如何填补?
许多工厂的流程漏洞如同“隐形漏斗”:采购计划与生产需求脱节、质检标准执行偏差、设备维护被动响应。
特变电工的改造极具代表性。该企业曾因投标评审流程繁琐错过多个重大项目。引入CRM系统后,投标文档自动关联历史项目数据,评审委员会通过可视化看板实时查看技术可行性、成本核算等维度评分。系统还能模拟不同报价方案的利润空间,帮助决策层在1小时内完成复杂标书评估。这一变革使报表统计成本降低70%,人员效率提升40%。
在汽车零部件领域,东华转向系统公司通过QMS(质量管理系统)实现全流程品控。每件产品都带有唯一编码,生产过程中超过200个检测点的数据实时上传云端。当某批次产品的不良率异常升高时,系统自动追溯至具体工序、操作员及原材料批次。这套体系使质量成本降低20%,客户投诉率下降45%。
三、生产柔性如何实现?
个性化定制与规模化生产的矛盾,曾是制造业的“不可能三角”。但智能管理系统正在打破这一魔咒。
黑湖科技小工单系统在中小工厂的应用令人耳目一新。某五金加工厂过去依赖纸质工单,急单插单时经常出现物料错配或设备冲突。接入系统后,车间看板实时显示设备负载率,工人通过手机APP抢单,系统自动匹配技能认证与计费规则。当客户临时要求更改零件尺寸时,工艺参数自动同步至相关机床,避免传统模式下需要停工调整的损失。该工厂人均管理设备数从1.5台增至3台,订单交付周期缩短40%。
更宏观的案例来自上汽大通C2B模式。用户可通过在线平台自定义车辆配置,系统即时分解出3000多个零部件需求,并联动供应商调整排产计划。这种“用户驱动制造”的模式,使单车生产成本降低18%,订单交付周期从28天压缩至21天。
给制造业者的三个行动指南
1. 诊断先行:梳理核心痛点,优先解决影响成本占比超15%的环节,如某纺织厂通过能耗监测系统发现空压机耗电占比达24%,改造后年省电费超200万元。
2. 小步快跑:选择模块化系统,例如先上线库存管理模块验证效果,再逐步扩展至生产排程、设备运维等领域。
3. 人才筑基:培养“懂工艺+通数据”的复合型团队,某阀门厂设立“数字化专员”岗位,负责将老师傅的经验转化为系统算法,使新产品调试周期从2周缩短至3天。
高效赋能智能制造工厂管理软件精准管控助力降本增效,绝非简单的技术堆砌,而是通过数据穿透、流程重构和资源重组,让工厂的每个细胞都焕发“智能生命力”。当管理系统真正成为生产的“神经中枢”,制造业的提质增效之路将越走越宽。